Металлорежущий инструмент
Под определением «инструмент» понимают технологическое орудие целевого назначения, необходимое для изменения состояния предметов труда. Металлорежущий инструмент применяют для работы с металлозаготовками, в процессе которой он послойно снимает излишки материала, придавая заготовке нужную форму. На выходе получаем либо готовое изделие, либо же полуфабрикат для дальнейшего производства. В металлургической и металлообрабатывающей промышленности инструменты разделяют на группы: станочные, ручные, контрольно-измерительные, режущие.
В последнюю категорию попадают состоящие из крепежной, режущей и калибровочной части инструменты. Режущая часть включает заточенное лезвие (несколько лезвий), посредством которого внедряется в тело заготовки и срезает слои. До конца позапрошлого века на изготовление инструментов шла исключительно углеродистая сталь, но к началу ХХ
столетия ее заменил быстрорежущий высоколегированный железный сплав. Из последних достижений наших дней к наиболее важным можно отнести технологию нанопокрытия. Благодаря ней мы получили износостойкие сверла, фрезы, резцы и прочие инструменты, способные работать при высоких скоростях.
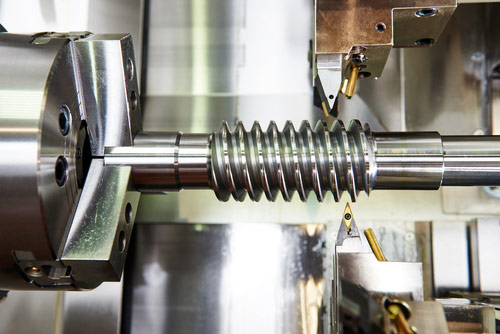
Кроме лезвия в режущей части находятся канавки для стружки, стружколоматели, каналы для поступления охлаждающей жидкости. Калибрующая область восполняет режущую при переточках.
Резцы по металлу
Резец – самый простой и востребованный инструмент для работы по металлу. Состоит из главного режущего ребра, способного обтачивать, растачивать, делать прорези, обрабатывать плоские и фасонные поверхности. Материал, из которого сделан резец, должен быть гораздо прочнее, чем у заготовки. Во избежание хрупкости ему придают более вязкую структуру, и он не выкрашивается в процессе эксплуатации. Широкое распространение имеют радиальные токарные резцы. Станок подает инструмент перпендикулярно оси обрабатываемой заготовки, и стружка сходит по передней поверхности стержня резца.
Для данной разновидности инструментов очень важно обладать высокой механической прочностью и устойчивостью к истиранию.
Фрезы для металлорежущих станков
Автоматизированное производство нуждается в высокопроизводительном инструментарии для обработки заготовок. С этой стороны фрезерование опережает строгание резцами на уровне серийной промышленности. В общем виде фреза – это тело вращения, состоящее из нескольких лезвий, также позволяющее послойно работать с металлом. Принцип действия характеризуется высокоскоростными оборотами инструмента и медленной его подачей. Для работы с цилиндрическими деталями, плоскостями, фасонным металлопрокатом подача станка должна быть прямолинейно-поступательной.
Цилиндрические фрезы с винтовыми зубьями нужны для оборудования горизонтально-фрезерных станков. Их производят из высоколегированной стали вкупе с твердосплавными пластинками.
Торцевыми фрезами с режущей кромкой оснащают вертикально-фрезерные станки. У данной разновидности инструмента профилирующими служат лишь верхушки режущих кромок лезвий. Торцовым кромкам отведена вспомогательная роль. Такая фреза имеет плавный ход при небольшом показателе припуска. Она может быть массивней и жестче в сравнении с цилиндрической, но это позволяет распределять и надежно монтировать режущие элементы. В случае необходимости можно паять к лезвиям профилактику из твердых сплавов.
Для фрезерования отверстий и канавок применяют дисковые фрезы, для наклонных плоскостей и пазов – угловые. Во время работы концевой фрезы главные лезвия на цилиндре исполняют задачу глубокого прохождения в материал заготовки. А лезвия, расположенные на торцах, лишь зачищают поверхность. Существуют также фрезы шпоночные, фасонные, для обработки Т-образных отверстий.
Сверла спиральные
Сверло также причисляют к категории металлорежущих инструментов. Оно необходимо для реализации цилиндрических отверстий в заготовках. Спиральное сверло – самая востребованная модификация в промышленном производстве. По телу рабочей его части проходят две спиральные колеи, отводящие стружку и также образующие режущую поверхность.
Стойкость к изнашиванию для всех металлорежущих инструментов рассчитывается в минутах, потраченных на работу между переточками.