Заточка инструмента
Крупные машиностроительные предприятия, задействованные в сфере металлообработки по мере износа режущего инструмента, осуществляют его заточку. Стоит отметить, что происходит это централизованно на специальных заточных станках. Данная процедура крайне важна для производительной работы станочного оборудования. Однако на небольших предприятиях или в ремонтных мастерских, где нет возможности и необходимости содержать специальные заточные подразделения, заточку инструмента осуществляют самостоятельно. Заточку инструмента рекомендуется производить в отдельных помещениях оборудованных вытяжкой для удаления абразивных частиц образующихся в процессе выполнения данных работ.
При ручной заточке инструментов используют специально предназначенные для этого точильно-шлифовальные станки. Обычно их оснащают подручниками для установки резцов, требующих заточки, или же поворотным столиком. В процессе ручного затачивания, резец опирается на станочный упор, а обрабатываемая поверхность прижимается к шлифовальному кругу.
Качество выполнения заточки инструмента напрямую зависит от технологических характеристик шлифовального круга и, конечно же, от квалификации рабочего.
Правилом хорошего тона считается перемещение резца по подручнику или столику относительно затачивающей (рабочей) поверхности круга, для его равномерного изнашивания.
Токарные резцы в зависимости от их конструкции и степени износа обычно затачивают по передней, задней либо по обеим поверхностям.
Так, стандартные виды резцов из быстрорежущей стали или оснащенные твердосплавным материалом чаще затачивают по всем рабочим поверхностям. Если передняя часть резца в результате обработки изношена незначительно, то заточка проходит исключительно по задней поверхности.
При заточке инструмента стоит учитывать тот факт, что чрезмерное усилие прижатия режущего инструмента к точильному кругу, может спровоцировать возникновение нежелательных трещин и прижогов.
При заточке инструмента ему нужно давать возможность остыть, причём стоит избегать резкого охлаждения, погружая его в воду тем местом, которое затачивается.
Неплохим способом охлаждения будет заточка нескольких инструментов сразу. При этом каждый инструмент затачивается до незначительного разогрева, после чего кладется на массивную металлическую плиту, где он медленно отдаёт тепло, а в это время берётся следующий инструмент и так далее.
При заточке свёрл следует помнить, что углы φ
, образующиеся между режущей кромкой и осью вращения инструмента должны быть одинаковы для каждого зуба. Не маловажным здесь будет и равенство геометрических параметров задних поверхностей, которые рекомендуется затачивать, предавая последним криволинейную форму. Для чего сверло прижимают к абразивному точильному кругу и одновременно поворачивают.
Поперечная кромка сверла имеет отрицательные передние углы и не участвует в резке металла, соскабливая его. С целью снижения сопротивления движению подачи для сверл диаметром более 15
миллиметров поперечную кромку подтачивают на шлифовальном круге малого диаметра.
Обычно свёрла затачиваются вручную, но если требуется, наиболее точная и производительная заточка сверл, то их отдают в специализированные заводские отделения, где имеются соответствующие заточные станки.
Важно понимать, что заточенная поверхность сверла из инструментальной стали не должна иметь трещин и прижогов. Как и в случае с резцами, затачивание требует максимальной концентрации внимания и высококвалифицированного подхода.
Правила безопасности при заточке режущего инструмента
Столь ответственная и травмоопасная процедура как заточка инструмента должна производиться в точном соответствии с основополагающими принципами, а именно:
• В первую очередь, работник должен убедиться в полной исправности заточного станка. Проверить механизмы и устройства, в том числе шлифовальные круги и кожухи.
• Зазор между подручником (или поворотным столиком) должен составлять не более 3
миллиметров.
• Подручник (поворотный столик) устанавливают по высоте таким образом, чтобы точка соприкосновения обрабатываемой поверхности режущего инструмента с поверхностью точильного круга находилась либо на уровне оси шпинделя, либо чуть выше, при этом, не превышая 10
миллиметров.
• Угол раскрытия кожуха точильно-шлифовального станка не должен превосходить 90°
. При этом обязательно нужно учитывать, что угол раскрытия по отношению к горизонтальной линии должен составить не более 65°
.
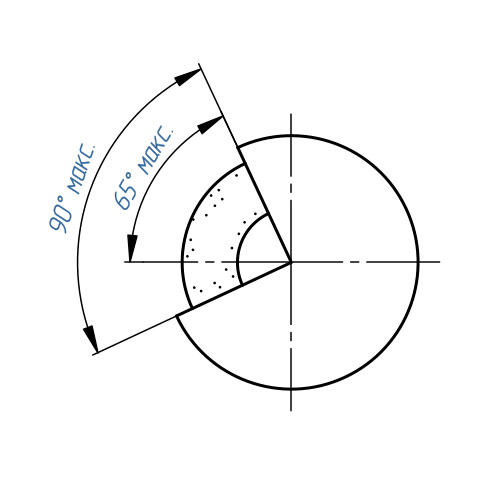
• Направление вращения круга должно соответствовать тому, чтобы затачиваемый инструмент прижимался к подручнику (поворотному столику), а искры летели строго вниз.
Кроме того, техника безопасности подразумевает обязательное использование защитных очков или опускание защитного экрана станка при выполнении работ по заточке.